A Step-by-Step Guide to Implementing ANSI Z359.2 for Fall Protection in Entertainment Venues

In the world of entertainment, safety behind the scenes is often as critical as the performances on stage. From rigging to lighting, technicians work at dangerous heights, making a comprehensive fall protection program essential. The ANSI Z359.2 standard provides a detailed framework for establishing and maintaining a robust fall protection program. If you’re looking to implement a compliant fall protection system for your venue, here’s a step-by-step guide to help you get started.
Step 1: Designate a Fall Protection Program Administrator
The first step in implementing a fall protection program is appointing a Fall Protection Program Administrator. This individual will be responsible for overseeing the program development, implementation, and ongoing management.
Key Duties:
- Develop fall protection policies.
- Organize training sessions.
- Monitor compliance with both OSHA and ANSI standards.
- Document all fall protection-related activities.
By having a dedicated administrator, you ensure that someone is always focused on maintaining the highest safety standards for your team.
Step 2: Develop a Written Fall Protection Program
Next, create a written plan that serves as the foundation of your fall protection program. This document should detail every aspect of how fall protection will be managed.
What to Include:
- Define work areas where fall protection is required (e.g., catwalks, garages, gates).
- Clarify responsibilities for each role involved in the program (Administrator,Competent Person, Authorized Persons).
- Identify the fall protection equipment to be used (guardrails, harnesses, fall arrest systems).
- Establish rescue procedures for incidents involving falls.
- Detail how inspections and training records will be maintained.
This plan will be the go-to resource for ensuring consistent and effective fall protection measures.
Step 3: Conduct Hazard Assessments
Once the program is in place, it’s time to conduct a hazard assessment. A thorough
assessment identifies all potential fall hazards and determines which fall protection
measures are needed.
How to Perform Assessments:
- Inspect elevated workspaces, such as grids, lighting platforms, and traps in stages.
- Identify potential hazards, such as unguarded edges or improper anchor points.
- Consider ways to eliminate the need for working at height, when possible.
Hazard assessments are critical to understanding where fall protection systems should be installed and what risks need mitigation.
Step 4: Select Appropriate Fall Protection Systems
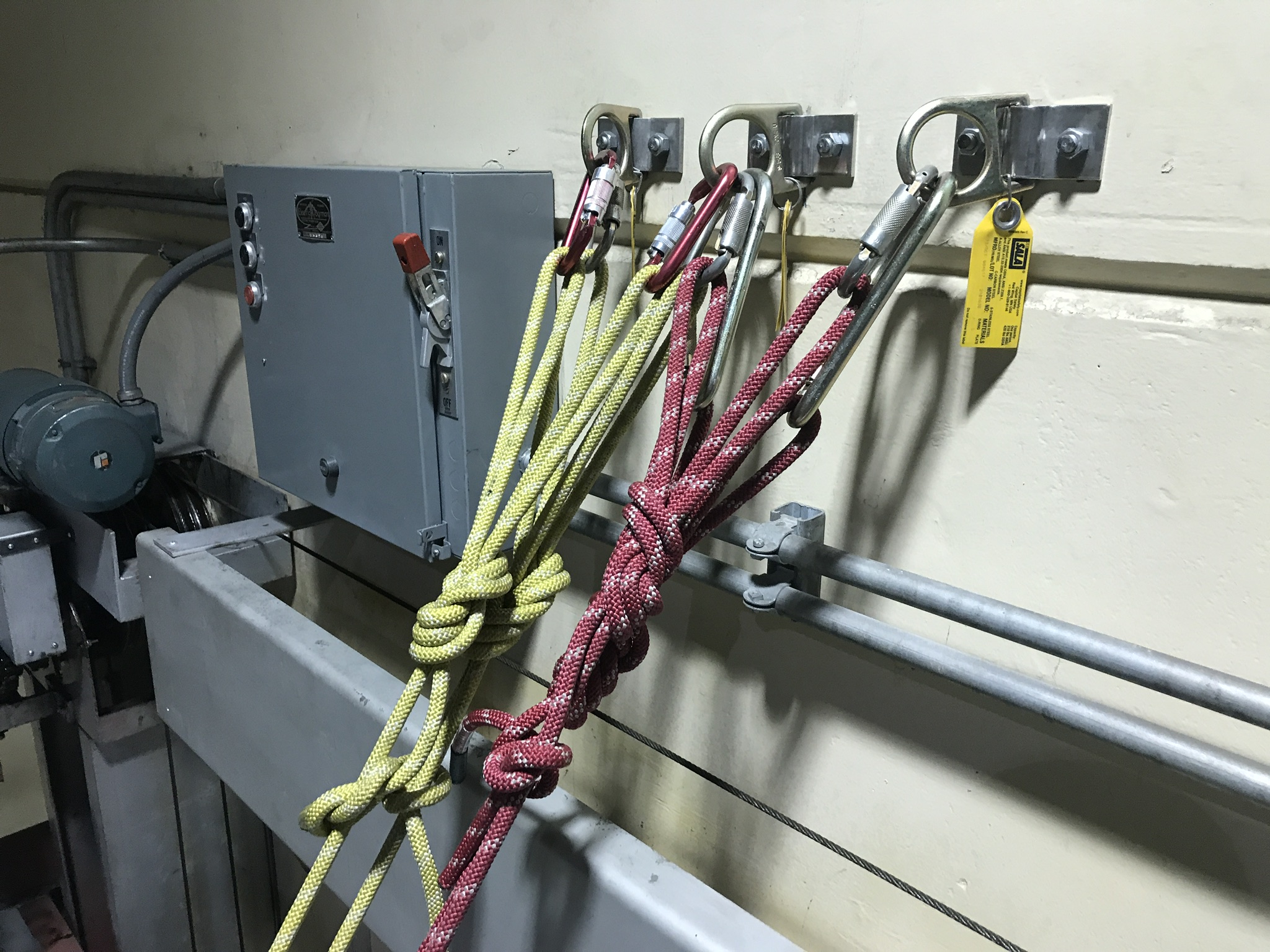
Based on the results of the hazard assessment, select the most suitable fall protection
systems using the Hierarchy of Controls:
- Elimination: Can the task be done without working at height?
- Passive Fall Protection: Install guardrails or barriers.
- Fall Restraint Systems: Prevent workers from reaching a fall hazard.
- Fall Arrest Systems: Use systems that stop a fall in progress, such as personal fall arrest systems (PFAS).
Choosing the right systems ensures the highest level of safety for technicians, whether they’re working on scaffolds, lighting rigs, or catwalks.
Step 5: Install and Inspect Fall Protection Systems
Once you’ve selected your fall protection systems, it’s crucial to install them properly
and conduct regular inspections.
- Installation: Ensure that all systems—whether they are permanent guardrails or temporary fall arrest systems—are correctly installed and meet OSHA and ANSI Z359.2 requirements.
- Inspection: Inspect all fall protection equipment before use, checking for damage or wear. Regularly scheduled inspections by qualified personnel should be part of the program.
Proper installation and maintenance help prevent equipment failure and ensure your systems are always ready when needed.
Step 6: Train Key Personnel
ANSI Z359.2 mandates specific training for all personnel involved in fall protection, from the administrator to those using the equipment. Make sure to properly train:
- Program Administrator: Oversees the overall fall protection system.
- Competent Person: Inspects equipment and identifies hazards.
- Authorized Persons: The workers who will be using fall protection equipment.
Training Topics:
- Hazard recognition.
- Proper use of fall protection systems.
- Rescue procedures and emergency response.
- Equipment inspection and maintenance.
Training should be documented and regularly refreshed to keep up with new standards or changes in the work environment.
Step 7: Develop and Implement Rescue Plans
A comprehensive rescue plan is crucial for any fall protection program. If a fall occurs, quick and efficient rescue procedures must be in place to minimize injury or harm.
Rescue Plan Essentials:
- Identify the rescue methods that will be used (e.g., self-rescue, assisted rescue, technical rescue).
- Train workers to use rescue equipment, such as ropes and lowering devices.
- Conduct rescue drills regularly to ensure readiness.
Proper rescue planning can save lives in an emergency, so make sure your team is trained and prepared to respond.
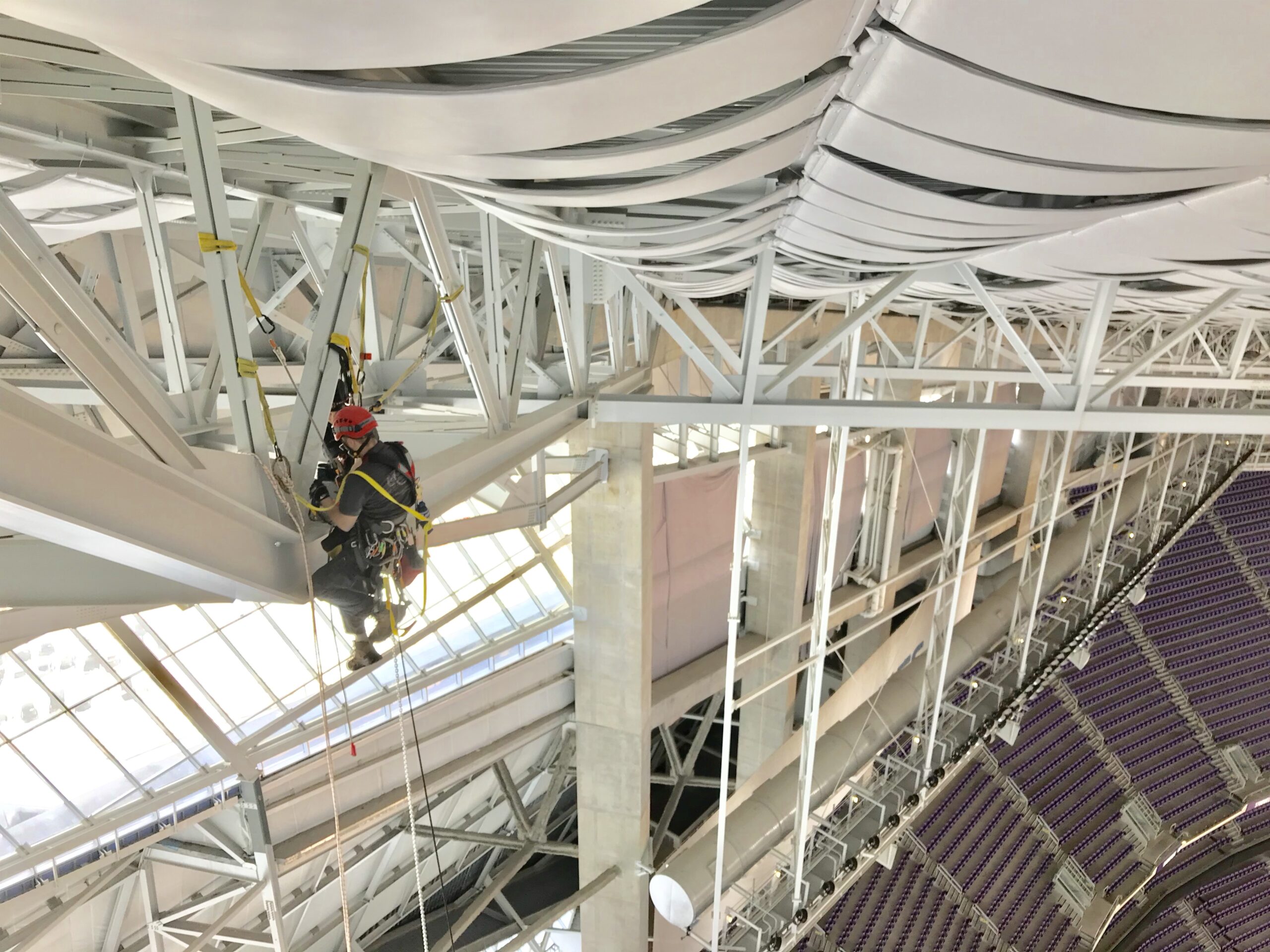
Step 8: Inspect Equipment Regularly
Fall protection equipment must be regularly inspected to ensure it’s in good working condition. This step is crucial for preventing accidents due to faulty or worn-out gear.
Inspection Guidelines:
- Daily Checks: Inspect equipment like harnesses, lanyards, and anchor
points before every use. - Periodic Inspections: Conduct more in-depth inspections periodically, as
specified by ANSI Z359.2.
By keeping a strict inspection schedule and retiring any damaged equipment, you can ensure the safety of everyone working at height.
Step 9: Conduct Program Audits and Evaluations
Regular audits are essential to maintaining the effectiveness of your fall protection
program. Audits should assess whether the program is being followed correctly and
whether it needs any adjustments.
Audit Focus Areas:
- Review training records to ensure that everyone is up-to-date.
- Ensure that fall protection equipment is being inspected and maintained.
- Evaluate rescue procedures through regular drills.
Auditing your program helps identify areas for improvement and ensures compliance with ANSI Z359.2 and OSHA regulations.
Step 10: Continuously Improve the Program
Fall protection programs are not static—they should evolve with new technology,
changing work environments, and updated safety regulations.
Continuous Improvement:
- Update your written program as new hazards are identified.
- Incorporate new equipment and technologies into training programs.
- Review incidents or near-misses to refine procedures.
By continuously improving your program, you ensure it remains effective and adaptable, providing long-term safety for your team.
Conclusion
Implementing a fall protection program based on ANSI Z359.2 is an essential step in ensuring the safety of technicians working at height in entertainment venues. By following these 10 steps, you’ll create a robust and compliant system that not only meets legal requirements but also fosters a culture of safety. Whether your team is rigging lights, working on scenery, or maintaining operating stage lifts, a well- implemented fall protection program will help protect them and keep operations running smoothly.
All photos provided by Trevor Whipkey
Back to Home
Editor's Note: At StageLync, an international platform for the performing arts, we celebrate the diversity of our writers' backgrounds. We recognize and support their choice to use either American or British English in their articles, respecting their individual preferences and origins. This policy allows us to embrace a wide range of linguistic expressions, enriching our content and reflecting the global nature of our community.
🎧 Join us on the StageLync Podcast for inspiring stories from the world of performing arts! Tune in to hear from the creative minds who bring magic to life, both onstage and behind the scenes. 🎙️ 👉 Listen now!